The following write up explains the difference between the Quality Assurance and the control Quality.
Quality is the degree to which a set of inherent (existing) characteristics fulfils requirements. ISO 9000
Quality Assurance
A set of activities that ensure quality in the processes by which end products are developed.
Quality Assurance (QA) is the procedure used to generate the deliverables. It focuses on scheduling, documenting, and supporting the certain course of actions that are essential to assuring quality. The process carries out at the beginning of a project and draws on specifications according to company standards. The results of the quality assurance planning activities are quality strategies, review and test plans, an assortment of tracking tools, and training individuals for specific techniques and procedures. The primary purpose of QA is to avert any shortcomings. It’s a management practice used to guarantee a specific level of quality for an enterprise.
“part of quality management focused on providing confidence that quality requirements will be fulfilled.” ISO 9000
Undertaking quality assurance at the very beginning of a project is the key to alleviate the identified risks. Besides, communication plays a significant role in managing project risk and is essential for realizing efficient QA. Some prominent examples of quality assurance include project audits, checklists, strategy and guidelines development. Auditing is an essential part of the quality assurance that helps in comparing definite settings with defined requirements and report to the management. The auditor may use review techniques as an assessment tool. Though it doesn’t involve in corroboration activities that result in either acceptance or rejection of the final product. An audit leads to the evaluation of the procedure and controls covering the assembly and verification activities.
The Manage Quality process involves performing systematic quality activities and uses quality audits and failure analysis to determine which processes should be used to achieve the project requirements, to meet the quality objectives of the project, and to ensure that activities and processes are performed efficiently and effectively. Kim Heldman 9th Edition
QA aims to emphasize on the process that is used to create the product. It significantly helps in enhancing development and test procedures so the flaws don’t arise when the project is complete. Additionally, it formulates a quality management system and the evaluation of its competence. Deterrence of quality issues through deliberate and methodical activities include documentation. Statistical tools and techniques are applied to quality assurance in processing inputs and functional parameters.
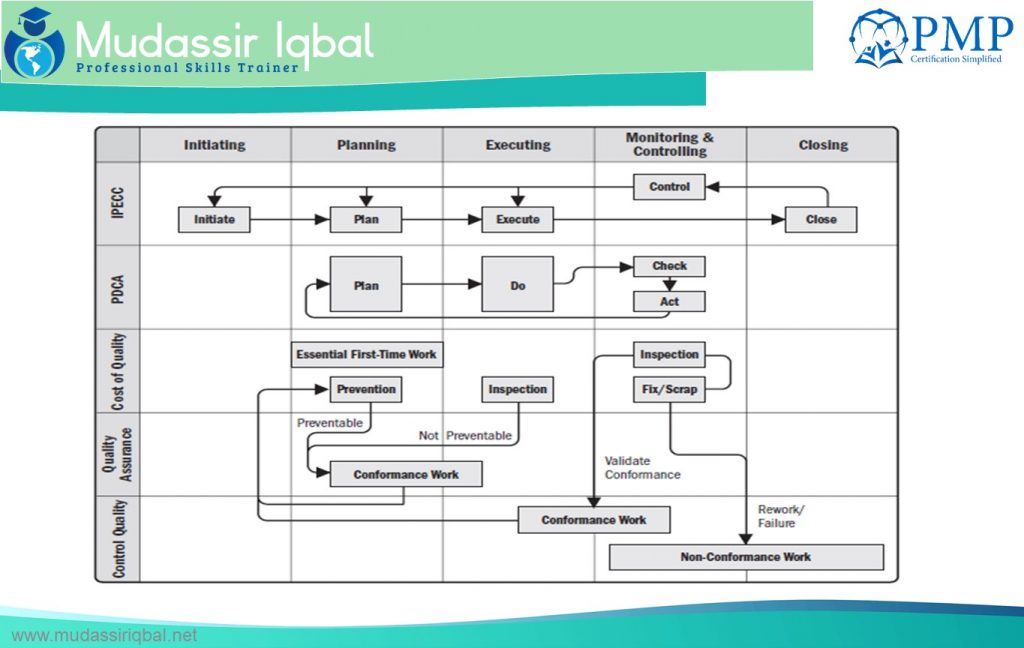
Control Quality
A set of activities that ensure quality in products. The undertakings focus on classifying issues in the real products produced.
Quality Control (QC) are quality associated activities with the conception of project deliverables. It is used to authenticate that deliverables are of standard quality and they are complete. It involves activities that are intended to identify the level of quality of the distributed solutions. Quality control comprises of functional strategies and activities used to accomplish requirements for quality. These procedures are settled with stakeholders before project work has started.
Quality control includes confirmation of productivity to anticipated quality levels. The solutions are checked against client requirements with diverse checks being directed at planned points throughout the project. Project team use a variety of techniques and carry out testing and inspections to make sure the final project meets the approved set of requirements. QC activities include review, deliverable peer evaluations, and testing procedure.
“part of quality management focused on fulfilling quality requirements.” ISO 9000
QC purposes to determine defects in the complete product. It aims to identify issues after a product is complete and prior to its release. These activities or strategies are used to accomplish and maintain product quality, procedure, and service. Quality control is the responsibility of particular team members who test the products. When statistical tools and techniques are executed to final products, this is known as statistical quality control.
Quality control is all about following the defined requirements. It has no concern with the particular requirements of the product being developed. QC activities are carried out after the completion of the product. On the contrary, the activities involved in quality assurance are identified before the completion of the project and while the project is in the developing phase.
Examples:
In a factory producing pencils, a quality control manager will count the number of faulty pencils before they leave the production phase. These items and then measured and rejected. On the other hand, a quality assurance manager will evaluate the results of pencils and recommend improvements accordingly.
Consider another example of a software development project, the quality control manager will test the code once it is written. While the quality assurance manager develops consistent code blocks and makes sure that all resources are in place to progressively create the best quality product. Moreover, quality control includes the measurement of shortcomings in the final production line and quality assurance involves the procedure that identifies improvements within the process.
Comparison Quality Control vs Quality Assurance
The quality assurance relates to how a process is performed or how a product is made, quality control is more the inspection aspect of quality management.**
Quality Assurance or Manage Quality
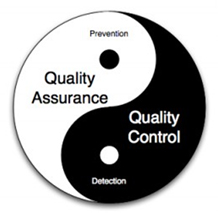
- Process-related
- Proactive
- Audit
- Prevention
- Project Managerial function
- Quality Verification
- Creating Deliverables
Quality Control
- Product related
- Reactive
- Check
- Inspection
- Independent Organizational function
- Quality Validation
- Verifying Deliverables
QC is used to verify the Quality of the output;
QA is the process of managing for quality.
Benefits of Quality Management
- The high-quality output which confirms the requirement and fit for use.
- They increase the efficiency of operations by removing the waste from the processes
- They provide customer satisfaction, which affects your brand and helps in growing your business.
- Conformance of Quality helps brand retention and brand awareness.
- They encourage a high level of confidence and a motivated team
Further Readings
- Project Quality Management
- Executing Process Group
- Monitoring and Controlling Process group
- QUALITY CONTROL & QUALITY ASSURANCE**
- The Difference Between Quality Assurance and Quality Control
[pt_view id=”c356c37lza”]